لوله مانیسمان چیست؟ کاربرد و انواع آن
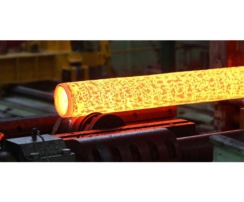
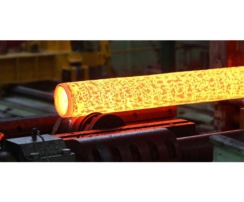
لوله ها تجهیزاتی هستند که برای انتقال سیالات، تولید مخازن تحتفشار، صنایع نظامی و کاربردهای وسیع دیگری مورد استفاده قرار میگیرند. در زبان انگلیسی لولهها را معمولاً با دو لغت پایپ و تیوب معرفی میکنند. از نظر ظاهری هر دو لغت به معنی لوله هستند ولی از نظر کاربرد و محل استفاده متفاوتاند. در این مقاله به بررسی لوله مانیسمان و ویژگیها، کاربردها و قیمت لوله مانیسمان میپردازیم. شما میتوانید برای دریافت اطلاعات بیشتر و قیمت انواع آهن آلات با شمارههای موجود در سایت تماس بگیرید.
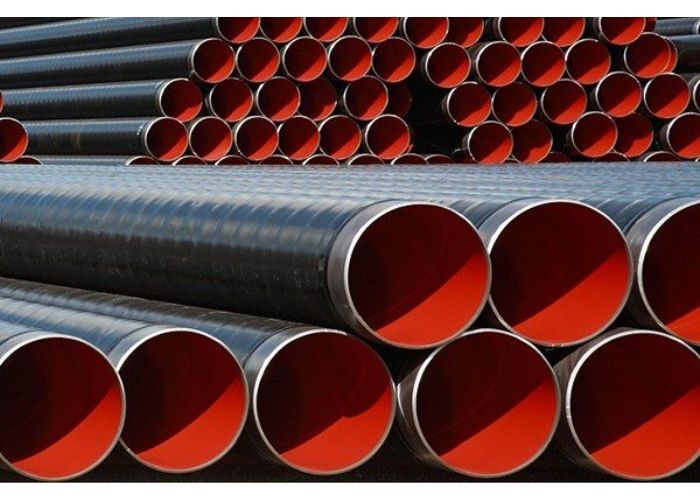
لوله مانیسمان چیست؟
در ابتدا به بررسی دو لغت پایپ و تیوب میپردازیم. پایپ به لوله هایی اطلاق میشود که وظیفه انتقال سیال از نقطهای به نقطه دیگر را بر عهده دارند اما تیوب به لوله هایی اطلاق میشود که وظیفه گردش سیال در داخل یک سیستم را بر عهده دارند.
لولهها از جنبههای مختلفی مانند جنس، کاربرد و فرایند تولید دستهبندی میشوند. آنها از نظر جنس به دو دسته کلی لوله های فلزی و غیرفلزی تقسیم میشوند. از لوله های فلزی پرکاربرد میتوان به لوله های فولادی، چدنی، مسی، آلومینیومی، لوله مانیسمان و سربی و از لوله های غیرفلزی پرکاربرد میتوان به لوله های پلیمری، شیشهای، بتنی و سفالی اشاره کرد.
فرایند تولید لولهها باتوجهبه جنس آنها میتواند متفاوت باشد. بهعنوانمثال لوله های پلیمری معمولاً به روش اکستروژن پلیمری و تزریق پلاستیک، لوله های سفالی بتنی به روش قالبگیری، لوله های شیشهای به روش قالبگیری شیشه مذاب و لوله های فلزی عموماً به روش اکستروژن تولید میشوند.
لوله فلزی
لوله های فلزی به یکی از دو شکل زیر تولید شدهاند:
لوله های درزدار که با انواع جوش مستقیم یا مارپیچ، شکلگرفتهاند و لوله های بدون درز یا مانیسمان.
همانطوری که از اسم این مقاطع برمیآید، تفاوت اساسی لوله های فلزی در نحوه تولید آنهاست. همانطور که میدانید حتی اگر فرایند جوشکاری در لوله های درزدار بادقت زیادی انجام بشود و جوش لوله بسیار مستحکم باشد، بازهم مشکلاتی مانند ترک خوردن یا آسیبدیدگی از قسمتهای جوشکاری آغاز خواهند شد. این یعنی یک لوله درزدار در بهترین حالت ممکن بازهم بهاندازه یک لوله بدون درز قدرت و استحکام ندارد.
لوله درزدار
لوله های درزدار لوله هایی هستند که از جوش لبهگرد شده یک ورق پس از عبور از غلتکهای متعدد تولید میشوند و به دو دسته درزدار مستقیم و درزدار مارپیچ تقسیمبندی میشود. لوله های با درز مستقیم عموماً به علت سختی تولید و استحکام پایینتر، در محدوده قطرهای کوچکتر مورد استفاده قرار میگیرد. در مقابل لوله های با درز مارپیچ به دلیل مزیتهای زیر کاربردهای وسیعتری دارند. برتریهای این لولهها نسبت به انواع درزدار مستقیم شامل موارد زیر میشود:
- در محدوده وسیعی از لحاظ قطر و ضخامت قابل تولید هستند.
- شکل نهایی آنها بادقت زیاد و بدون نیاز به فرایندهای نظیر کالیبره کردن حاصل میشوند و به همین علت جوشکاری و نصب آنها سادهتر است.
- توزیع تنش در آنها خیلی یکنواختتر از لوله هایی با جوش طولی است. بهعبارتدیگر توزیع انرژی در اطراف جوش یکنواختتر است و خواص مکانیکی همگنتری ایجاد خواهد شد که به دنبال آن مقاومت لوله در برابر شکست بیشتر میگردد.
- لولهها با درز مارپیچ در برابر ضربه، فشار زیاد و تغییرات درجه حرارت مقاومت بیشتری از خود نشان میدهند.
- لوله های درزدار برای انتقال سیالاتی چون آب و فاضلاب، نفت و گاز در فشار مورد استفاده قرار میگیرند.
لوله بدون درز
این لولهها بدون ناپیوستگی سطحی و داخلی هستند و بهصورت یک مرحلهای تولید میشوند. این لولهها به دلیل استحکام و دقت زیاد تولید، معمولاً در انتقال مواد با دما و فشار بالا، انتقال مواد اسیدی و سمی مورد استفاده قرار میگیرند. از مصارف این لولهها میتوان به لوله های تحتفشار انتقال نفت و گاز، مخازن بویلرها، کمپرسورها و بهعنوان اجزای مکانیکی گردنده مانند پوسته برینگها و اکسل خودرو، لوله تفنگ و تانک در صنایع نظامی اشاره کرد.
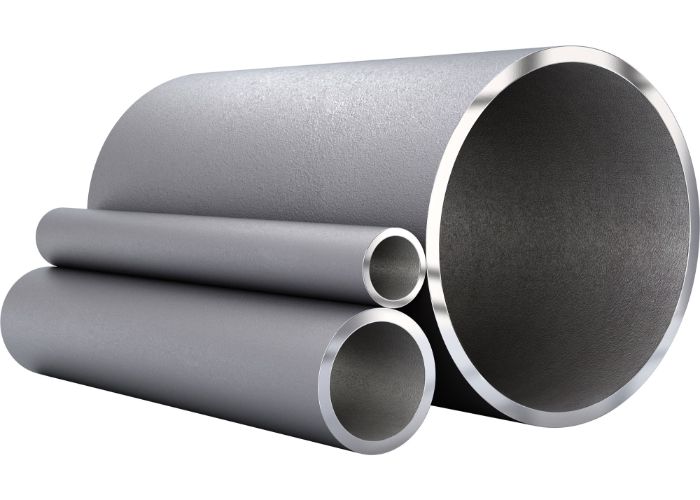
تولید لوله مانیسمان
لوله بدون درز یا مانیسمان با فرایند جوش تولید نمیشوند. تولید این نوع از لولهها در پایان قرن نوزدهم توسعه یافت. علیرغم بسیاری از آزمایشهای قبلی، اختراع فرایند سوراخ کردن یا سنبه زنی متقاطع لوله بدون درز توسط برادران مانسمان تا پایان سال 1880 به طور گستردهای بهعنوان نشانهای از شروع تولید مقیاس بالا تولید لوله های بدون درز شناخته شده است.
یک بخش از فرایند تولید، سوراخ کردن شمش محور نورد موازی با محور آن است. با چرخش در همان جهت، این نورد یک مسیر اسپیرال برای عبور شمش از طریق شکاف رول ایجاد میکند. علاوه بر این، سرعت خروج در حدود 10 برابر سرعت دورانی غلتک کاهشیافته است.
با معرفی یک هسته سنبه مانند که در فاصله بین غلتکها قرار گرفته است، مواد اولیه جامد دوار را میتوان برای ایجاد یک پوسته توخالی در حین نورد گرم توسط عمل غلتککاری و گردش همزمان سوراخ کرد. بااینحال هنوز نمیتوان لوله های با ضخامت دیوارههای معمولی را در طول دلخواه توسط فرایند سوراخکاری و سنبه زنی بهتنهایی تولید کرد.
بعد از معرفی یک فرایند شکلدهی مجدد، تولید لوله های فولادی بدون درز توسط برادران مانیسمان امکان پذیر شد. توسعه غلتک فرمدهی نیز یک تکنولوژی غیرمعمول و نوآورانه بود که در آن پوسته توخالی ضخیم شده دیواره، به شکل لوله های نازک از طریق عملیات نورد کشیده میشوند که بر روی سنبه قرار میگیرند بدینوسیله عمل توخالی سازی تکمیل شده و شمش بهصورت لوله بدون درز تبدیل خواهد شد.
هم اکنون لوله های بدون درز (مانیسمان) از شمش گرد تولید میشوند که از طریق سنبه زدن مرکز سوراخ شدهاند تا پوسته توخالی ایجاد شود و سپس نورد یا اکسترود شده و بهاندازه مدنظر کشیده میشود.
مراحل ساخت لوله بدون درز
- تولید پوسته لوله توخالی در فرایند سنبه زنی یا اکستروژن
- پنل لوله توخالی را با کاهش قطر و ضخامت دیواره کشیده شود
- تولید یک لوله نهایی در روند نورد گرم یا سرد
این فرایند تولید شامل هیچ جوشکاری نیست و لوله بدون درز (مانیسمان) قویتر و قابلاعتمادتر میشود. لوله بدون درز در مقابل فشار پایداری بیشتری نسبت به سایر لولهها از خود نشان میدهد.
فرایند تولید لوله مانیسمان
در طی این عملیات شمشها در یک کوره چرخشی به دمای 1250 تا 1300 درجه سانتیگراد گرم میشوند. قبل از این کار شمشها با فشار آب تمیز شده و به کارخانه سوراخکاری با سنبه منتقل میشوند تا در آن شمش سوراخ شده و پوسته توخالی ضخیم دیوار تولید کنند. سپس این شمش خام اولیه را به طول 1.5 تا 2 برابر طول اولیه آن میکشد و سطح مقطع بین 33 تا 50 درصد کاهش مییابد.
کارخانه سوراخکاری دارای دو نورد غلتکزنی مخصوص کشیدن لوله است تا در همان جهت چرخش هدایت شوند. محورها در حدود 3 تا 6 درجه نسبت به خط نورد افقی قرار دارند و فاصله بین غلتکها عموماً توسط یک غلتک پشتیبانی در بالا و یک کفی پشتیبانی در پایین بسته شدهاند.
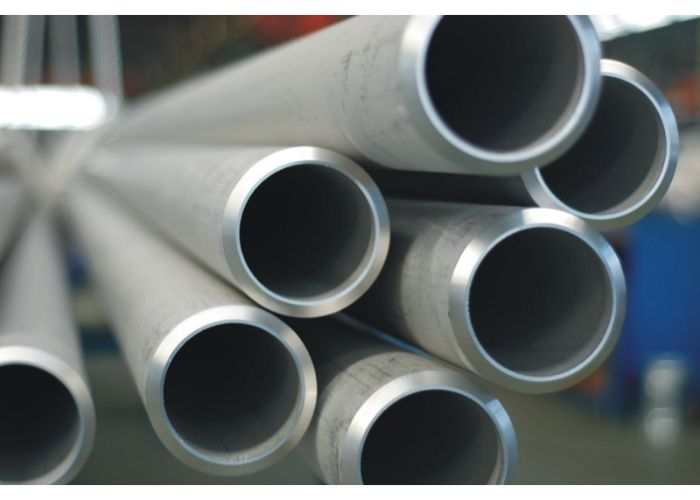
مرحله سنبه زنی
یک نقطه سنبه زنی مانند یک ابزار داخلی در مرکز شکاف رول واقع شده و بهوسیله یک بلوک رانش خارجی توسط یک هسته سنبه مانند در موقعیت مرکز قرار گرفته است. پوسته توخالی با دیواره ضخیم پس از عملیات سوراخ کردن مجدداً در ایستگاه پلانگر غلتکزنی میشود تا تولید لوله را به پایان برساند. نسبت طول دهی در طی فرایند غلتکزنی بین 5 الی 10 درصد است و با کاهش مقطع حدودی 80 الی 90 درصدی همراه خواهد بود.
فرایند پلانگر
خط غلتکزنی دارای دو غلتک است که گاهی بهخاطر عمل پرسی بهعنوان قالب شناخته میشود و با شکل مخروطی در اطراف غلتک. غلتکها به سمت حرکت متقاطع مواد خام تنظیم میشوند. دمای کاری بین 200 الی 220 درجه برای اطراف غلتکها قرار دارد و شامل ورودی مخروطی شکل، یک سیلندر و یک همسطح کننده است که در یک محفظه بزرگتر برای آزاد کردن قطعه کار قرار دارد. فرایند غلتکزنی یک فرایند فورجینگ نوردی مرحلهای است که با چرخش قطعه به عقب و جلو عمل میکند.
پس از اتمام فرایند پلانگر یا غلتک فرم دهنده، لوله نهایی شده از سنبه خارج شده و بخشی از پوسته توخالی بریده میشود. پس از حرارت دادن آن در یک کوره، لوله بهاندازه مناسب در خط نورد کاهش مییابد. نورد تولیدکننده یک قطر خارجی دقیق را تولید میکند و همچنین باعث افزایش مرکزیت و دوار شدن لوله خواهد شد. این فرایند معمولاً شامل سه مرحله با دو یا سه غلتک دقت بالا است.
نورد یک سیکل عبور بسته را (در تنظیمات چندین ایستگاه) تشکیل میدهد که هرکدام از آنها یک زاویه را با خط نورد قبلی تنظیم میکنند.
در نورد کاهشی یا کششی، قطر خارجی لوله به طور قابلملاحظهای کاهشیافته و ضخامت دیواره مقداری افزایش یا کاهش مییابد. بسته به نوع محصول خروجی، کارخانهها دارای 5 الی 28 مرحله نورد هستند.
مرحله نهایی تولید
پس از آخرین عملیات فرمدهی، لولهها به پایان خط میرسند و در یک بستر کاهش دمایی، خنک میشوند و پس از آزمایشهای نهایی به بخش تکمیل منتقل خواهند شد که در آنجا عملیاتهایی مانند ماشینکاری پایان لوله، هموارسازی و آزمایشهای هیدرولیکی انجام میشود.
در مورد لوله های با قطر بزرگ معمولاً از یک شمش چند ضلعی استفاده میشود. این شمش پس از حرارت دادن در یک کوره دوار ابتدا به یک مدور با سنبه عمودی وارد میشود. شمش جامد توسط یک پانچ استوانهای تحت پرس قرار گرفته و حدود نیمی از قطر سوراخ ایجاد شده و یک پوسته توخالی با یک پایه بسته تولید میشود.
مراحل بعد شامل کاهش ضخامت دیواره همراه با درجه کمی از کشیدگی طول لوله در نورد است. در طول این فرایند، انتهای لوله سوراخ شده است. سپس پوسته توخالی در خط غلتک فرم دهنده شکل لوله را به خود میگیرد و عملیات اندازهگیری و برش صورت میپذیرد.
فرایند نورد پلاگین یا فرایند کشیدن
فرایند نورد توپیزنی برای نورد کردن لوله های بدون درز در بازه قطر 60 الی 406 میلیمتر با ضخامت دیواره از حدود 3 الی 40 میلیمتر و طول لوله بین 12 الی 16 متر استفاده میشود. این خط سوراخکاری در یک مرحله انجام میشود تا یک پوسته توخالی دیوار نازک ایجاد شود که طول آن 3 الی 4.5 برابر طول اصلی آن خواهد بود و سطح تغییرات 65 الی 75 درصد است.
خط سنبه زنی دارای دو غلتک پیشران است که دارای یک مسیر گذر دوطرفه است. محورهای غلتک، موازی با خط نورد هستند و از 6 الی 12 درجه به سمت افقی حرکت میکنند.
این کفشکهای هدایتکننده به روند کشش کمک میکنند و بهعنوان غلتکهای ثابت عمل میکنند، بهطوریکه قادر به تولید یک پوسته توخالی نازک هستند. محصولی که از غلتک بیضوی عبور میکند خط نورد را دنبال کرده و به سنبه این اجازه را میدهد تا بهعنوان یک ابزار داخلی عمل کند تا لوله را به طور مؤثری تشکیل دهد.
باتوجهبه زاویه نسبتاً زیاد شیب غلتک و سرعت نورد بالا، سرعت خروج محصول به میزان قابلتوجهی تسریع مییابد. این عمل جهت افزایش طول عمر سنبه بسیار حائز اهمیت است. در ارتباط با لوله های با قطر بزرگ قبل از اتصال توپی، یک سنبه ثانویه (که بهاصطلاح کشنده نامیده میشود) وجود دارد.
سنبههای جدید فقط یک بخش سوراخکاری مخروطی با غلتکهای کاری با طراحی دو جهت دارند چرا که آنها هرکدام در حدود 30 درجه با محصول در حال تولید زاویه دارند و 10 الی 12 درجه نسبت به خط افق مورب هستند. فاصله موجود در نورد با دو دیسک جانبی که آن دو نیز متحرک هستند بسته شده است.
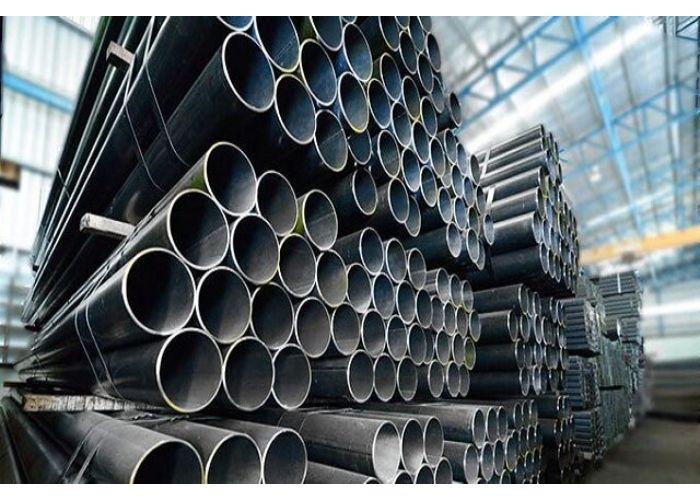
فرایند نورد مداوم
پس از برداشتن سنبه، لوله های نورد قبل از پردازش دوباره گرم میشوند. کارخانه کشش که در تولید و سازوکار مشابه کارخانه نورد است از 12 غلتک پایه بلند درست شده است.
کاهش تنش تکنیکی منحصربهفرد است به این دلیل که بدون استفاده از یک تکیهگاه و نگهدارنده سنبه ضخامت دیواره را کاهش میدهد درحالیکه قطر لوله نیز همزمان کاهش مییابد. نیروی کششی که لوله در بین آن قرار میگیرد نهتنها در کاهش ضخامت دیواره لوله مؤثر است بلکه کاهش قطر انجام شده در هر مرحله را میتوان تا 3 برابر زیاد کرد.
فرایند کاهش و اندازهگیری برای لوله های با قطر کوچک استفاده میشود. ازآنجاکه سوراخ کردن، نورد و برش لوله هایی با قطر کوچک اقتصادی نیست، تولید لولهها با نورد گرم با قطر کمتر از حدود 75 میلیمتر نیاز به یک فرایند کاهش و اندازهگیری دارد که در آن یک دستگاه ویژه کار میکند. این دستگاه مشابه خط نورد مداوم است. این ترکیب از 8 الی 16 مرحله شامل 2 غلتک با شیارهای بلند به قطر 305 میلیمتر تشکیل شده است.
برای قطرهای در حدود 140 میلیمتر و بالاتر، اندازهگیری جهت اطمینان از اندازه و گرد بودن یکنواخت در طول لوله صورت میگیرد؛ پس فرایند اندازهگیری صرفاً شامل عبور لوله از طریق 2 یا 3 پایه غلتک اندازه است که شیارهای آن کمی کوچکتر از لوله حلقه شده است. در بعضی موارد، گرمکردن دوباره موردنیاز است.
گاهی نورد و چرخش با فرایندهای معمولی یعنی نورد مداوم جایگزین میشوند، برای مثال با 9 پایه پشتیبان جداگانه از غلتکهای شیار بلند تا پس از سوراخ کردن یک قطعه توسط خط سنبه زنی، یک سنبه روانکار که به میزان قابلتوجه بزرگتر از پوسته سوراخ شده است، وارد شود و هر دو از خط نورد عبور کنند.
فرایند نورد مداوم شامل چندین غلتک در یک سری از نوردهای چرخشی است تا یک خط نورد شکل بگیرد. این نوع نورد پوسته توخالی را که در خط سنبه زنی سوراخ شده را میکشد و توسط یک سنبه که بهعنوان ابزار داخلی عمل میکند به لوله فرم نهایی میدهد.
فرایندهای جدید اجرای عمل نورد
در فرایندهای جدید، عمل نورد در کارخانهها بهجای استفاده از سنبههای آزاد و شناور از مدلهای کنترل شده استفاده میشود. برتری این نوع فرایند این است که به طور مؤثرتری میلههای کوتاهتر و کمتری جهت تولید سنبه لازم است. به این نوع از فرایند نورد مداوم نیز بهعنوان خط تولید لوله با ایستگاههای چندگانه (MPM) شناخته میشود.
نورد لوله چندمرحلهای قسمتی از یک فرایند نورد گرم لوله بدون درز بهواسطه پوسته سوراخ شده است. این نورد معمولاً از 8 پایه از دو غلتک شیاردار تولید شده که با زاویه 90 درجه نسبت به هم تعبیه شدهاند. متریال تولید روی سنبه که خنک و روان شده سوار میشوند و در جایی که نورد شروع شده و در ایستاده اول فشار داده میشوند. سنبه در امتداد فرایند MPM با سرعت ثابت اجرا میشود. پس از آن لوله برش، کالیبره، آمادهسازی و کنترل قبل از ارسال انجام میشود.
با این فرایند، نهایت کشیدگی میتواند به دست آید. طول لوله تولید شده میتواند تا 30 متر نیز باشد. بدفرمی و عدم دوار بودن کمتر از 10٪ خواهد بود.
در صورت استفاده از فرایند نورد مداوم تا استخراج میله سنبه، دمای لوله حدوداً 500 درجه سانتیگراد کاهش مییابد. این لوله دوباره 950 الی 980 درجه سانتیگراد گرم میشود و سپس در نورد کاهشدهنده مورد کشش قرار میگیرد.
نورد کاهشدهنده
نورد کاهشدهنده و کشش میتوانند شامل هر تعداد غلتک بین 24 تا 28 ایستگاه یا بیشتر باشند و همه در فرم گرفتن خط نزدیک هم باشند. هر پایه دارای درایور یا موتورهای چرخنده متغیر خاص خود است و با 3 غلتک با کوچکترین قطر ممکن تعبیه شده است. 3 غلتک با هم یک مسیر نورد را تشکیل میدهند که بهتدریج از ایستگاهی تا ایستگاهی کوچکتر میشود. در این نورد از ابزار داخلی استفاده نمیشود و سرعت محیط غلتکها به طور مداوم از ورودی به انتهای خروجی نورد افزایش مییابد.
چندین روند تولید دیگر برای نورد کردن لوله بدون درز وجود دارد. این فرایندها شامل فرایند اعمال فشار، فرایند سوراخ و کشش، فرایند اکستروژن لوله و فرایندهای نورد متقاطع است. فرایندهای نورد متقاطع شامل مراحل نورد مارپیچ و روند نورد با قالب است. این لولهها با روشهای فرم دهی سرد، طراحی سرد و روش فرم دهی با قالب طی نورد سرد نیز تولید میشوند.
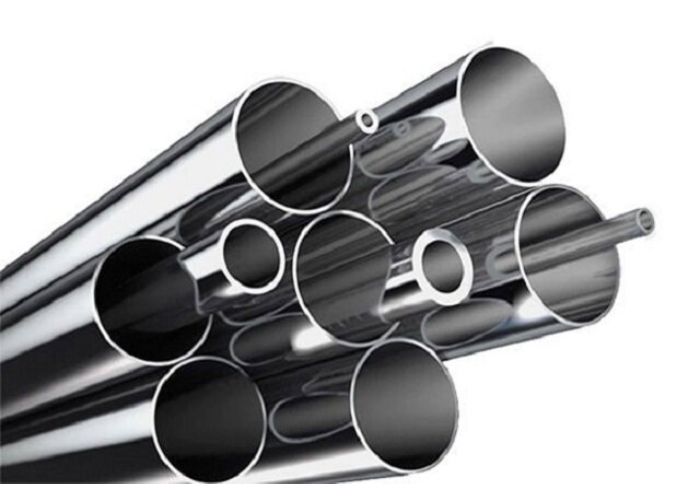
مشخصات لوله مانیسمان
لوله های مانیسمان با استانداردها و گواهیهای گوناگونی تولید میشوند و هر محصول باید بر اساس استانداردهای درج شده توسط کارخانه تولید شده باشد؛ در غیر این صورت آن لوله یک محصول استاندارد نیست.
دو استاندارد زیر معمولاً برای تولید لوله های بدون درز فلزی استفاده میشوند:
- لوله های فولادی از استاندارد ASME B36.10
- لوله های استیلی از استاندارد ASME B36.19
ارائهدهندگان این استانداردها، برای هرکدام از ویژگیهای یک لولة بدون درز، خصوصیاتی مانند قطر، ضخامت و طول، بازة خاصی را مشخص کردهاند؛ کارخانههایی که ادعا میکنند محصولات خود را بر اساس این استانداردها به بازار عرضه میکنند، حتماً باید لوله را در بازهها و ابعاد ازپیشتعیینشده، ارائه کنند.
ابعاد تولید لوله مانیسمان
ابعاد لوله های مانیسمان، تابعی از ضخامت یا ردة این محصولات است. لوله های بدون درز، در ردههای متعددی تولید و روانة بازار میشوند. سه روش زیر برای ردهبندی لوله های مانیسمان بکار میروند:
روش اول: مطابق با استاندارد ANSI B36 APL5L، لوله های مانیسمان باتوجهبه ضخامت خود، ردهبندی میشوند.
روش دوم: مطابق با استاندارد ANSI که از یک فرمول کلی حاصل میشود، لوله های بدون درز فولادی در 8 دستهبندی قرار میگیرند.
روش سوم: مطابق با وزن کلی، لولهها به سه گروه استاندارد (STD)، سنگین (XS) و فوق سنگین (XXS) تقسیم میشوند.
لوله های مانیسمان در ابعاد 6 و 12 متری تولید شده و قطر آنها بین 1.2 الی 36 میلیمتر است. طبیعتاً وزن این لولهها متناسب با طول، قطر و ضخامت، متغیر خواهد بود.
انواع لوله مانیسمان
انواع رایج لوله های مانیسمان به شرح زیر است:
رده 20: این لولهها ضخامتی در حدود 2 الی 6 میلیمتر و سایزی حدود 1 الی 12 اینچ دارند و وزن آنها بر اساس مشخصات دیگر تا حدود 300 کیلوگرم متغیر است.
رده 40: این نوع از لولهها ابعادی در حدود 1 الی 12 اینچ و ضخامتی در بازة 2 الی 10 میلیمتر خواهد داشت. وزن این لولهها گاهی تا 500 کیلوگرم هم خواهد رسید.
رده 60: این نوع از لولهها، مانند سایر انواع لوله، بدون درز نیستند و تقاضا برای آن کم است. این رده، معمولاً در بازة قطر 8 الی 24 اینچ تولید و عرضه میشوند و وزن آن بر اساس قطر و ضخامتشان متفاوت خواهد بود.
رده 80: در این رده لولهها ضخامتی بین 3 الی 9 میلیمتر و وزنی حدود 9 الی 150 کیلوگرم دارند. همچنین از نظر سایز بسیار متنوع هستند.
رده 120: وزن این لولهها در مقایسه با ضخامت زیاد آن تا حدود 700 کیلوگرم هم خواهد رسید و سایز و ابعاد آنها بر اساس درخواست مشتریان متنوع است.
رده 160: بالاترین ردة لوله های مانیسمان را شامل میشوند که با وزنی بسیار زیادتر از ردههای دیگر به بازار عرضه شدهاند.
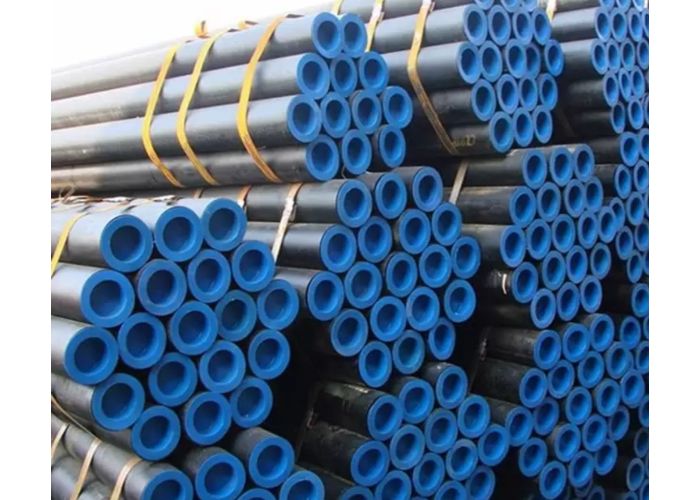
کاربرد لوله مانیسمان
این لولهها دارای کاربردهای ویژه و گستردهای شامل موارد زیر هستند:
- خطوط فشارقوی برق
- صنایع مربوط به غذا و دارو
- خطوط هیدرولیک
- انتقال نفت و گاز
مقایسه مشخصات فنی لوله مانیسمان با سایر لوله های صنعتی
این لوله های فولادی درزدار برای نصب در شرایط ویژه نظیر فشارهای عملیاتی بالا طراحی شدهاند. البته سایر لوله های صنعتی مانند لوله های پلیاتیلن و لوله های یوپیویسی (UPVC) هم قابلیت نصب در فشار معمولی و بالا را دارند اما بنا بر صلاحدید مهندسین باید از نوع به خصوصی از لوله و اتصالات در تأسیسات برق و مکانیک استفاده شود. لوله پوش فیت، لوله پلیاتیلن و لوله یوپیویسی اغلب برای انتقال آب و فاضلاب در تأسیسات مختلف استفاده میشوند. انواع لوله صنعتی جدا از کاربردهای مختلف آنها، دارای دیواره بسیار مقاومی هستند و میتوانند در برابر تغییرات شرایط محیط پایدار بمانند.
قیمت لوله مانیسمان
لوله های مانیسمان در چند سال اخیر بسیار پرطرفدار شدهاند و خود را جایگزین بسیاری از لوله های دیگر کردهاند. در سالهای اخیر قیمت لوله مانیسمان دچار نوسانات زیادی شده است اما لازم به ذکر است که این لولهها دارای کیفیت بالایی بوده و با استفاده از آن در هر فعالیت صنعتی میتوانید از موفقیت پروژه خود اطمینان حاصل کنید. تولید این لولهها در کشورهایی مثل هند، چین، ایران و آلمان انجام میگیرد و به دلیل نوسانات ارز و دلار دارای نوسان در قیمت است. قیمتگذاری لوله مانیسمان مانند دیگر لولهها با درنظرگرفتن یک سری از فاکتورهای مشخص مانند موارد زیر تعیین خواهد شد.
- وزن لوله
- ضخامت لوله
- ابعاد لوله
- سایز لوله
- کیفیت لوله
- شرکت سازنده لوله
- کشور تولیدکننده لوله
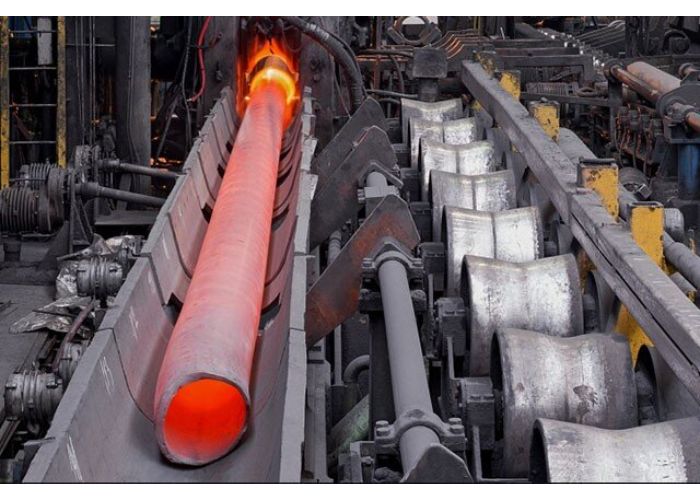
آزمایشهای فنی لوله مانیسمان
حتماً قبل از خرید این لولهها از نتایج آزمایشهای زیر اطمینان حاصل فرمایید. این نتایج میتواند کیفیت محصول خریداری شده شما را تضمین کند.
از جمله این آزمایشها میتواند به موارد زیر اشاره کرد:
آزمایش سختی لوله مانیسمان
در این آزمایش باید تمام مشخصات مکانیکی لوله مانیسمان را در نظر بگیرید. بهخاطر داشته باشید که فرایند تولید و برشکاری میتواند بر مشخصات مکانیکی ماده اولیه که استنلساستیل است تأثیر بگذارد. همچنین در انجام آزمایش سختی عملکرد و کیفیت لوله را نیز فراموش نکنید.
برای انجام آزمایش سختی دستگاه آزمایشکننده روی سطح لوله قرار داده میشود تا میزان تورفتگی و سایز آن را اندازهگیری کند. این آزمایشی سریع و آسان است اما برای برخی لولهها که دارای ناهمواریهای سطحی هستند یا رنگ آنها تیره باشد توصیه نمیشود.
در حال حاضر سه نوع آزمایش سختی وجود دارد:
- Luo
- Cloth
- Victoria
این آزمایشها با سه دستگاه راکول (Rockwell)، برنیل (Brinell) یا ویکرز (Vickers) صورت میگیرند که به ترتیب توانایی اندازهگیری مقادیر سختی HRB، HB یا HV را دارند. البته باید خاطرنشان کرد که نیازی به انجام هر سه آزمایش نیست و نتایج آزمایش سختی با یکی از این سه دستگاه کفایت میکند. البته دستگاه راکول نتایج دقیقتری دارد و میتوانید به نتایج بهدستآمده از آن اکتفا کنید. لازم به ذکر است که هزینه آزمایش سختی برای لوله های مانیسمان ضخیم پایینتر خواهد بود.
آزمایش کشش لوله مانیسمان
برای انجام آزمایش کشش، دستگاه لوله نمونه را تا حد شکستن میکشد. طی این فرایند دستگاه آزمایشکننده امکان اندازهگیری برخی مشخصات فیزیکی ازجمله استحکام کششی، استحکام عملکرد و میزان کشیدگی را خواهد داشت.
آزمایش فشار لوله مانیسمان
برای انجام این آزمایش دستگاهی مخروطی شکل را داخل نمونه لوله مانیسمان کرده و آن را منبسط میکنند. لوله مانیسمان باید حداقل 5 ثانیه این فشار را تحمل کرده و درنهایت نباید هیچگونه تَرک قابلمشاهدهای روی سطوح لوله به وجود بیاید. این آزمایش را اغلب از ضعیفترین قسمت لوله میگیرند و متوسط فشار قابلتحمل برای لوله مانیسمان 2.45 مگاپاسکال است.
آزمایش خوردگی لوله مانیسمان
یکی از ویژگیهای قابلتوجه لولهها تحمل آنها در برابر مواد اسیدی است. در این آزمایش اسید نیتریک استفاده میشود و غلظت آن به ترکیب فولاد مورد استفاده در تولید لوله بستگی دارد.
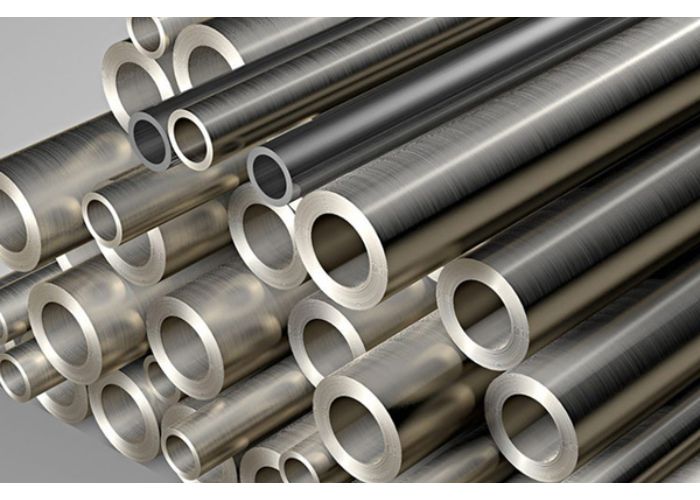
جمع بندی
لوله های مانیسمان به همراه لوله های درزدار جزو محصولات فولادی پرکاربرد قرار میگیرند. این لولهها در صنایع مختلفی مانند پتروشیمی، نیروگاهها و انواع آبرسانی کاربرد دارند و برای رفع نیاز مشتری، در ابعاد و اندازههای گوناگون تولید میشوند. برای دریافت مشاوره رایگان با استفاده از شمارههای درج شده در سایت با کارشناسان لایو آهن تماس بگیرید. قیمت انواع لوله، مثل قیمت لوله درز جوش و قیمت لوله گالوانیزه را نیز میتوانید با کمک جدول قیمت بروز دریافت کنید.
Warning: Undefined variable $post_id in /home/steely/public_html/liveahan/wp-content/themes/Ahanyar/comments.php on line 57
Warning: Undefined variable $post_id in /home/steely/public_html/liveahan/wp-content/themes/Ahanyar/comments.php on line 57
Warning: Undefined variable $post_id in /home/steely/public_html/liveahan/wp-content/themes/Ahanyar/comments.php on line 67
Warning: Undefined variable $post_id in /home/steely/public_html/liveahan/wp-content/themes/Ahanyar/comments.php on line 67
Warning: Undefined variable $commenter in /home/steely/public_html/liveahan/wp-content/themes/Ahanyar/functions/comments-callback.php on line 16
Warning: Trying to access array offset on value of type null in /home/steely/public_html/liveahan/wp-content/themes/Ahanyar/functions/comments-callback.php on line 16
Warning: Undefined variable $aria_req in /home/steely/public_html/liveahan/wp-content/themes/Ahanyar/functions/comments-callback.php on line 16
Warning: Undefined variable $commenter in /home/steely/public_html/liveahan/wp-content/themes/Ahanyar/functions/comments-callback.php on line 20
Warning: Trying to access array offset on value of type null in /home/steely/public_html/liveahan/wp-content/themes/Ahanyar/functions/comments-callback.php on line 20
Warning: Undefined variable $aria_req in /home/steely/public_html/liveahan/wp-content/themes/Ahanyar/functions/comments-callback.php on line 20